INSIGHT: SAF catalyst technology could also boost biochemicals production
Nazif Nazmul
20-Mar-2024
LONDON and BARCELONA (ICIS)–Catalyst technology used to power the first transatlantic flight conducted by a commercial airline which used 100% sustainable aviation fuel (SAF), could also have applications in chemicals production if a market can be developed to allow for commercial scale up.
The SAF used on the voyage, dubbed Flight100, was a SAF blend containing 88% HEFA hydroprocessed esters and fatty acids (HEFA) supplied by AirBP, the specialised aviation division of BP, and 12% SAK synthetic aromatic kerosene (SAK) supplied by Virent, a subsidiary of Marathon Petroleum Corporation.
Virent developed the SAK in conjunction with Johnson Matthey, using the latter’s proprietary BioForming sugars to aromatic process. Feedstocks such as sugar beet, sugar cane, and corn are currently used in the process, which is also capable of utilising cellulosic sugars as feedstock.
Current forms of SAF linked to HEFA and Fischer Tropsch Synthetic Paraffinic Kerosene (FT-SPK) require conventional jet fuel blending to enable an 8-25% aromatics presence to enable optimum fuel burning. Fossil-based conventional jet kerosene is blended with HEFA and FT-SPK based SAF to create a balance between the paraffins and aromatics required to ensure proper fuel system operations.
The BioForming sugars to aromatics process results in bio-based aromatics in the SAK, which enables up to a 100% drop in form of SAF, and can be compatible as a jet kerosene replacement. The SAK can also be blended with other types of SAF to boost the overall SAF content in the fuel mix.
The BioForming process could potentially play a vital role in helping scale up the much-needed global SAF capacity expansion required to meet the aviation sectors’ aim to reduce emissions.
The International Civil Aviation Organization (ICAO) adopted a global framework in November 2023, in which member states committed to strive towards reducing carbon emissions in international aviation by 5% by 2030 using SAF, low carbon aviation fuels, and other clean energy sources.
The EU is implementing a minimum SAF blend of 2% starting from 2025. Mandated SAF blending rates in airports across the bloc will increase to 6% by 2030, 20% by 2035, and 34% by 2040, eventually reaching 70% by 2050.
The US Department of Energy (DOE) published a plan that sees the country potentially meeting 100% of its projected jet fuel demand with SAF by 2050.
A 10% blending target by 2030 has also been set by the OneWorld airline alliance, which includes British Airways, American Airlines, Qatar Airways, Cathay Pacific, Malaysian Airlines, and others as members.
Currently, SAF makes up just over 0.1% in the global aviation fuel mix, which continues to be dominated by fossil-based jet kerosene.
Johnson Matthey must overcome any possible financial hurdles that may arise before it can scale up its BioForming technology.
Clariant was forced to shutdown its bioethanol plant in Podari, Romania, which also used cellulosic biomass as a feedstock. The company struggled to license out its Sunliquid technology while grappling to ramp up capacity of its bioethanol plant amid challenging operating economics.
Johnson Matthey and other companies spearheading technological developments in biofuels and bio-chemicals will have to consider lessons incurred from other projects and integrate such learnings into future plans.
BIOCHEMICAL FEEDSTOCK
POTENTIAL
According to David Kettner, president and
general counsel at Virent, this technology has
huge potential as a feedstock for chemicals
production because it can use a variety of
feedstocks to produce the sugars required for
the process. This includes lignocellulosic
sugars from woody biomass or agricultural
residues.
One third of the output of the process can be used for biochemical production and the company has already cooperated with companies such as Coca Cola where it produced bio-polyethylene terephthalate (PET) packaging.
Virent also cooperated with Japan’s Toray Industries to produce polymers which were used by the Patagonia clothing brand to produce a 100% bio-based polyester product.
The chemical feedstock produced by the process most closely resembles mixed xylenes.
“The stream itself looks very much similar to what you would see coming out of a reforming unit,” Kettner said. “You would take your mixed xylenes cut and be able to put it directly into existing processes for the production of benzene, toluene and xylenes, all of which have strong uses in polymer applications.”
He said a demonstration plant currently produces around one barrel/day of bio-reformate with the potential to scale up to commercial levels “very comfortably”.
Iain Gilmore, senior manager of Catalyst Technologies at Johnson Matthey added: “We are working at the moment with Virent and Marathon at commercializing the technology and we’re pretty confident we can get the size of plants up in the region of 300,000-400,000 tonnes/year of bio-reformate.
The project is going through the engineering and design phase, but is not yet at the stage where a formal announcement will be made.
Johnson Matthey and Virent have also developed a joint licensing model which is currently being taken to market, led by Johnson Matthey.
Insight by Nazif Nazmul and Will Beacham
Thumbnail photo: A 100% SAF-fuelled Virgin Atlantic flight (Source: Justin Lane/EPA/EFE/Shutterstock)
Global News + ICIS Chemical Business (ICB)
See the full picture, with unlimited access to ICIS chemicals news across all markets and regions, plus ICB, the industry-leading magazine for the chemicals industry.
Contact us
Partnering with ICIS unlocks a vision of a future you can trust and achieve. We leverage our unrivalled network of industry experts to deliver a comprehensive market view based on independent and reliable data, insight and analytics.
Contact us to learn how we can support you as you transact today and plan for tomorrow.
READ MORE
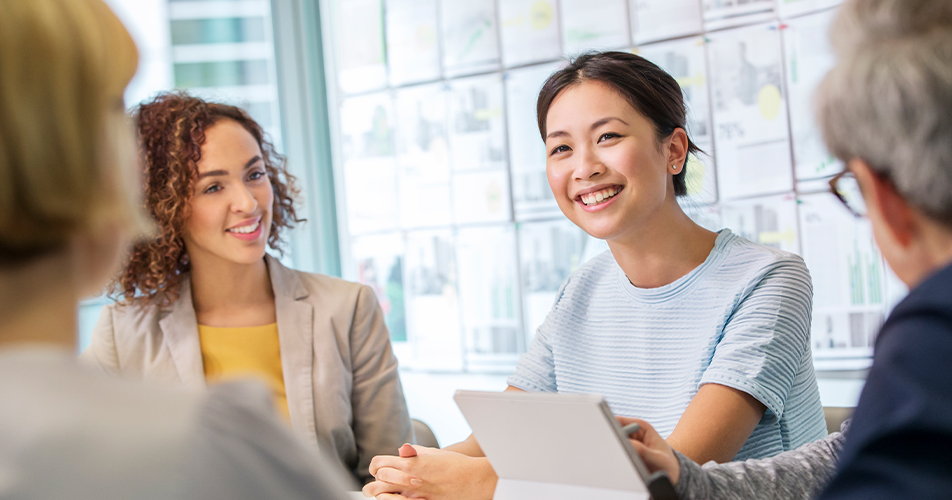